Step on board any Princess yacht and there is no denying the importance a master carpenter plays in the production of our craft. From beautifully finished bulkheads and doors, to expertly crafted furnishings, down to the wooden panels hidden beneath carpets and linings. Princess Yachts’ Carpentry Manufacturing Engineer, Justin Empson, explains how we combine technology with expert craftsmanship to create some of the finest yacht interiors in the world.
”My role at Princess is to support the Carpentry Department at KitParts by identifying opportunities for continuous improvement. This can involve anything from reviewing the way an individual item of furniture is put together through to assessing the quality and efficiency of the machinery and equipment used within the department. Having worked in the woodworking industry manufacturing high quality furniture for over 20 years, I have seen how technology has helped refine carpentry processes. Historically we manually cut parts from plywood patterns which were cumbersome to store, took time to locate and became worn over time, making them less reliable. Today, through the use of technology such as CNC (Computer Numerical Control) machines we can be more accurate and efficient with the way we fabricate parts.
We operate five CNC machines within KitParts. CAD (Computer Aided Design) drawings are converted into CNC files from which the machine can precisely cut a part to shape. We are also able to use the machine to mark up the placement of fixtures and fittings helping to streamline and improve accuracy during the assembly and fit out process.
We utilise ‘nesting’ software which looks at all the parts in the schedule that are due to be run through the CNC machine, and calculates how to cut the maximum number from a single sheet of material, reducing waste.
We use special purpose machinery which help to reduce what are otherwise very manual processes for our carpenters. As we produce hundreds of thousands of parts each year this saves a huge amount of time. This includes tools such as the Weinig CUBE which produces large volumes of precisely cut wood and the Edgebander which is used to add a veneer trim to raw plywood edges.
We have a team of skilled machine operators who utilise their knowledge and experience to assess the best tools to complete a part ready to be handed over to the Carpentry team for assembly. While technological advancements have undeniably helped with more efficient and accurate production, the assembly process is still heavily reliant on the skill of the individual carpenter. Timber is a living product so will always require refinement to ensure seamless joints and a high-quality finish.
Many of the joinery skills used by our Carpenters have changed very little over the centuries however, more advanced equipment has helped make the process easier and more efficient than more traditional methods.”

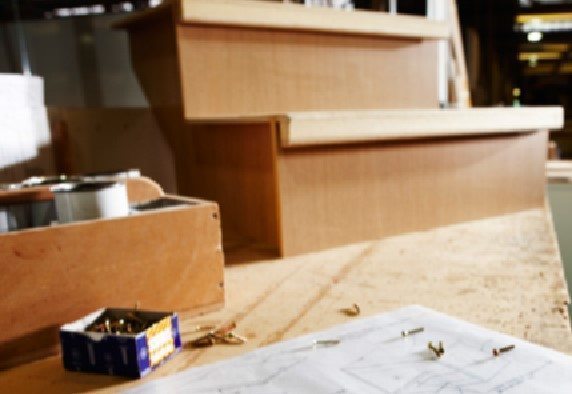